硅片作为半导体制造的基础材料,堪称半导体产业的基石。从日常使用的智能手机、电脑,到高端的航天航空设备、人工智能系统,几乎所有电子产品的 “心脏”—— 芯片,都源于硅片这一关键基础。
硅片加工是一个复杂且精细的流程,涵盖晶体生长、切割、研磨、腐蚀、抛光、清洗等诸多环节。每一个环节都对清洁度和精度有着近乎苛刻的要求,任何细微的瑕疵都可能在后续工序中被不断放大,最终影响芯片的良品率。
在这样的背景下,等离子清洗机作为一种创新性的干式表面清洗技术,在硅片加工中扮演着不可或缺的关键角色。它能够精准且高效地去除硅片表面肉眼不可见的微小污染物,为硅片加工的每一道工序提高洁净度,确保整个工艺流程的高精度、高质量推进,进而保障半导体器件的卓越性能与高可靠性。
等离子清洗机工作原理揭秘——物理与化学的协同作用
等离子清洗技术是利用了等离子体中这些活性粒子的特性,从而实现对硅片表面的高效清洗。其清洗过程包含物理轰击与化学反应两种主要机制,二者协同作用。
从物理层面来看,等离子体中的离子在电场加速下,以较高的动能撞击硅片表面。这种撞击力能够将硅片表面附着的微小颗粒、尘埃等污染物直接击飞脱离,就好比用高压水枪冲洗掉墙壁上的污垢一样。同时,离子的轰击还会对硅片表面产生一定的刻蚀作用,使表面变得微观粗糙,这不仅有助于后续工艺中其他材料在硅片上的附着,还能增大硅片的比表面积,提高其与后续处理物质的接触效率。
在化学反应方面,等离子体中的自由基发挥着关键作用。自由基具有极高的化学活性,它们能够迅速与硅片表面的有机物、氧化物等污染物发生化学反应。以硅片表面常见的有机油污为例,等离子体中的氧自由基会与油污分子发生氧化反应,将复杂的有机大分子逐步分解为二氧化碳、水等小分子挥发性物质,这些产物随后被真空泵抽离清洗腔室,从而彻底清除硅片表面的有机污染。同样,对于硅片表面自然形成的氧化层,氢自由基等活性粒子可以与之发生还原反应,将氧化硅还原为单质硅,恢复硅片表面的洁净度与活性。
等离子清洗机在硅片各环节加工中的卓越作
1.光刻胶去除,高效且无损
光刻胶在硅片加工中扮演着至关重要的角色,通过光刻工艺,将设计好的芯片电路图案精确地转移到硅片表面。在这一过程中,光刻胶依据其对特定波长光线的响应特性,在光照区域发生化学变化,使得后续显影步骤能够有选择性地去除部分光刻胶,从而在硅片上留下与掩膜版一致的精细图案,为刻蚀、离子注入等工序划定精准的 “施工蓝图”。
然而,当某一光刻层的任务完成后,光刻胶就需要被彻底清除,以便硅片进入下一阶段的加工流程。传统的光刻胶去除方法主要有化学溶剂浸泡法和边缘曝光法。化学溶剂浸泡法虽然成本相对较低、效率尚可,但存在诸多弊端。一方面,溶剂在浸泡过程中难以精确控制作用范围,极易喷洒到硅片中间的图形区域,对已形成的精细电路图案造成侵蚀,严重影响图形质量;另一方面,大量使用化学溶剂不仅耗材成本高,而且后续废液处理繁琐,对环境造成较大压力。边缘曝光法虽然在一定程度上提高了生产效率、降低了装置成本,但对于一些复杂形状的硅片或高精度要求的工艺,其曝光均匀性难以保证,容易导致光刻胶去除不彻底,影响后续工序的进行。
等离子清洗机在光刻胶去除环节展现出了卓越的性能优势。它采用干性处理方式,仅需引入少量氧气等反应气体进入等离子体反应系统。在强电场作用下,气体迅速电离形成等离子体,其中的活性氧原子与光刻胶中的碳氢化合物成分发生剧烈的氧化反应,将光刻胶迅速分解为一氧化碳、二氧化碳和水等挥发性气体,这些气态产物随即被真空泵抽离反应腔室,从而实现光刻胶的彻底清除。与传统方法相比,等离子清洗机提高硅片生产效率,整个去胶过程精准可控,能够有效避免对硅片表面图形的损伤,确保硅片表面无划痕、无残留,极大地提高了产品质量。同时,由于不使用酸、碱、有机溶剂,不仅降低了原材料成本,还从根本上杜绝了废液排放带来的环境污染问题,是一种绿色环保的先进去胶技术。
2.石墨舟清洗,保障镀层质量
在 PECVD(等离子增强化学气相沉积)工艺中,石墨舟凭借其出色的热传导性能、较小的热膨胀系数(与硅片相近,能有效避免热应力对硅片造成损伤)、良好的化学稳定性(不易与镀膜介质发生反应,确保镀膜过程稳定、硅片表面质量优良)以及较高的结构强度(保证硅片在加工过程中的稳定性和精度),成为 PECVD 工艺中承载硅片的不二之选。
然而,在 PECVD 工艺长期运行过程中,硅片表面沉积的氮化硅薄膜会不可避免地在石墨舟表面残留。随着残留氮化硅的逐渐积累,石墨舟的导电和导热性能会受到严重影响。这将导致在后续的镀膜工序中,硅片周围的电场分布不均匀,使得氮化硅镀层的厚度出现偏差,无法达到预期的均匀性要求;同时,温度控制也会变得不稳定,部分区域温度过高或过低,进而影响氮化硅镀层的质量和性能,降低太阳能电池片的光电转换效率。
真空等离子清洗机通过充入特定气体,经过物理和化学的一系列反应,实现对石墨舟表面的深度清洁。经过等离子清洗处理后,石墨舟表面的氮化硅残留得以高效清除,其导电和导热性能恢复如初,确保了后续 PECVD 工艺中硅片氮化硅镀层的高质量沉积,显著提高了生产良率。与传统的湿法清洗相比,后者不仅清洗效率大幅提升,而且避免了湿法清洗带来的长时间浸泡、化学腐蚀、废液处理等问题,切实保障了石墨舟的使用寿命和加工性能。
3.表面预处理,提升亲水性与粘附性
硅片表面的特性如亲水性和粘附性,对后续诸多工艺步骤的成败起着关键作用。在光刻、镀膜、键合等工序中,若硅片表面过于疏水,溶液或镀膜材料难以在其表面均匀铺展,会导致光刻图案的分辨率下降、镀膜厚度不均匀、键合强度不足等问题,严重影响半导体器件的性能与可靠性。例如,在光刻过程中,光刻胶溶液需要在硅片表面形成一层均匀、平整的薄膜,如果硅片表面亲水性差,光刻胶溶液就容易出现团聚、流淌不均的现象,使得曝光后的图形精度大打折扣,进而影响芯片的电路布局精度。
等离子清洗机能够对硅片表面进行精准的预处理,有效改善其表面性质。当等离子体与硅片表面接触时,一方面,等离子体中的离子轰击作用会使硅片表面微观结构变得粗糙,增加了表面的比表面积,为后续物质的附着提供更多的 “着力点”;另一方面,等离子体中的活性自由基,如氧自由基、氢自由基等,会与硅片表面的硅原子发生化学反应,引入羟基、羧基等极性官能团。这些极性官能团具有较强的亲水性,能够显著增强硅片表面对水及其他极性物质的润湿能力,使得溶液在硅片表面能够均匀、快速地铺展。同时,在镀膜或键合工艺前,经过等离子清洗处理的硅片表面,由于化学键合活性的提升以及微观粗糙度的优化,与镀膜材料或键合对象之间的粘附力得到极大增强,确保了镀层的牢固度和键合的紧密性,为后续复杂工艺的顺利实施奠定了坚实基础,有力保障了半导体器件的高性能与高可靠性。
等离子清洗机与传统清洗方法大比拼
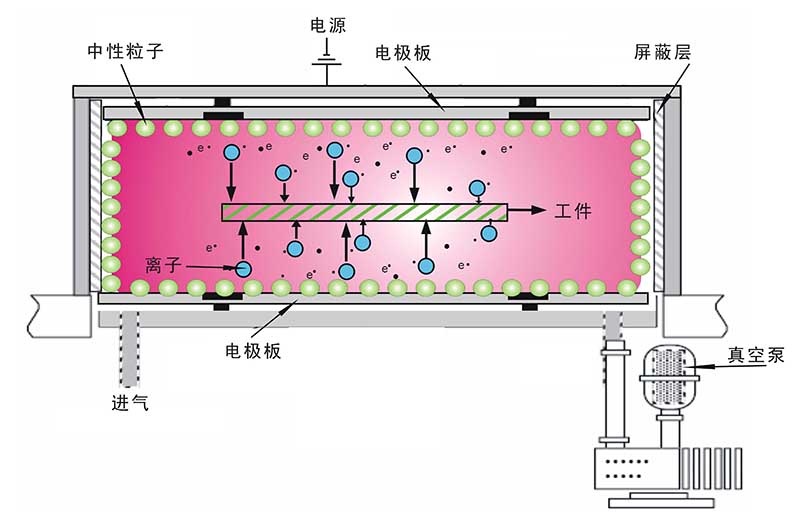
清洗效果:深度与广度的优势
在硅片清洗领域,传统湿法清洗长期占据主导地位,它主要依赖化学溶剂的浸泡、喷淋以及超声辅助等手段,借助化学溶解、物理冲刷等作用去除硅片表面污染物。然而,随着半导体技术向更高精度、更微小制程迈进,传统湿法清洗的局限性愈发凸显。在微观层面,对于硅片表面亚微米甚至纳米级别的微小颗粒,湿法清洗往往力不从心。这些微小颗粒可能由于静电吸附、化学键合等作用紧紧附着在硅片表面,化学溶剂难以渗透到颗粒与硅片的接触界面将其彻底溶解清除,即使配合超声振动,仍有大量颗粒残留,严重影响后续光刻、镀膜等工艺的精度。
等离子体对硅片的表面清洗则展现出卓越的微观清洗能力。等离子体中的离子以高速撞击硅片表面,能够将微小颗粒从硅片表面直接剥离,即便颗粒藏身于硅片表面的微观凹槽、缝隙等复杂结构中,也难以逃脱离子的轰击。同时,等离子体中的自由基与硅片表面污染物发生化学反应,将有机大分子分解为小分子挥发性物质,从根源上清除污染,确保硅片表面达到前所未有的洁净度,为高精度半导体工艺筑牢根基。
成本效益:长期与短期的考量
从短期来看,传统湿法清洗设备初期投资相对较低,对于一些资金有限、生产规模较小的企业具有一定吸引力。然而,若将目光放长远,湿法清洗的综合成本会更高。一方面,湿法清洗需要持续大量消耗化学溶剂,这些溶剂不仅采购成本高昂,而且使用后的废液处理成本更是惊人。为达到环保排放标准,企业需配备专业的废液处理设备,对废液进行中和、过滤、蒸馏等一系列复杂处理,每一步都耗费大量人力、物力与财力。
等离子清洗机虽然设备购置成本相对较高,但在长期运行过程中,其成本优势逐渐显现。它无需使用大量化学溶剂,仅需通入少量反应气体,运行成本大幅降低。同时,由于不产生废液,企业无需承担高额的废液处理费用,也减少了因环保不达标而面临的罚款风险。此外,高效清洗能力减少了硅片在清洗环节的停留时间,提高了生产效率,进一步摊薄了单位生产成本,为企业带来可观的经济效益。
环保特性:绿色清洗的典范
在环保意识日益增强的当下,传统湿法清洗因大量使用化学溶剂,成为半导体产业中的 “污染大户”。许多化学溶剂,如强酸、强碱以及有机挥发性溶剂,具有强腐蚀性、毒性和挥发性,在使用过程中极易挥发到空气中,对车间空气质量造成严重污染,危害操作人员健康;而清洗后的废液若未经妥善处理直接排放,其中的重金属离子、有机物等污染物会对土壤、水体生态系统造成毁灭性打击,引发一系列环境问题。
等离子体的环保清洗作为一种绿色干洗技术,完美契合环保需求。它在清洗过程中不使用有害化学溶剂,仅依靠等离子体中的活性粒子与污染物发生作用,避免了溶剂挥发带来的空气污染。而且,清洗产生的副产物主要为二氧化碳、水等无害气体,以及少量易于处理的固态微尘,这些产物无需复杂处理即可达标排放,从源头上杜绝了废液污染,为半导体产业的可持续发展开辟了新路径,是当之无愧的环保典范。
等离子清洗机的选型要点——依据需求精准抉择
制造业设备升级,等离子清洗机的适配选择至关重要,这需要综合考量多方面因素。首先,硅片尺寸是关键要素之一。若加工的是小尺寸硅片,如用于一些小型传感器、分立器件制造的硅片,常压型的表面处理机或许就能满足需求,其紧凑的结构、便捷的操作,既能节省实验室或生产车间的空间,又能保证稳定的清洗效果。而对于大尺寸硅片,常见于大规模集成电路制造,就必须选用容量更大的设备型号,其真空腔体足以容纳整片硅片,确保在清洗过程中硅片各部位都能均匀接受等离子体的作用,避免出现清洗死角。
另外,产能需求同样不容忽视。对于大规模量产型企业,高产能是首要追求目标。此时,工业自动化中等离子清洗机的集中和应用,应优先考虑具备高速处理能力的设备,这类设备往往配备了大功率的射频电源,能够在短时间内激发高强度的等离子体,快速完成硅片的清洗任务;同时,其真空系统的抽气速率也较高,可大幅缩短单个清洗周期,实现单位时间内更多硅片的处理,满足生产线的高效运行需求。相反,对于研发机构或小批量生产的场景,灵活性和多功能性更为重要,一些可灵活调整工艺参数、具备多种气体适配功能的中低端机型,既能满足不同实验方案对硅片清洗的个性化要求,又能有效控制设备成本。
此外,工艺要求的精细程度直接决定了设备的技术选型。若硅片加工工艺对表面粗糙度、亲水性等微观性质有极高要求,如高端芯片制造中的光刻前置工序,就需要选择频率精确、等离子体能量分布均匀的设备。通常,高频能量(如 13.56MHz )在此类场景中表现出色,其产生的等离子体活性粒子能量相对较低且分布均匀,能在精准去除污染物的同时,对硅片表面进行精细的微观调控,避免过度刻蚀等不良影响,确保硅片表面达到近乎完美的状态,为后续复杂且高精度的芯片制造工艺筑牢根基。而对于一些对表面精度要求相对不那么苛刻,但侧重于大面积清洗、快速去除厚层污染物的应用场景,低频(如 40KHz)则凭借其较强的物理轰击能力,能够高效地将硅片表面附着的顽固颗粒、厚层有机杂质等剥离清除,展现出独特的优势。